JTI
With negative pressure up to 20,000 cigarettes - per minute!
It was in 1908, when the first slim tobacco products left the cigarette factory of Heinrich and August Neuerburg. The two brothers recognised the signs of the times at the beginning of the 20th century: Modern cigarettes were the new tobacco trend and surpassed the previously popular cigars. Today, the cigarette production in Trier is under the label of JT International Germany GmbH - a German subsidiary of JT International SA, subsidiary of Japan Tobacco Inc. with well-known brand names such as Camel, Benson & Hedges or Winston.
The number of the day is 20,000.Today, modern machines produce 20,000 cigarettes per minute. “This is a very demanding process that needs to be mastered safely,” says Arnhelm Köster, Head of Industrial Engineering at JTI in Trier. The Trier plant produced 50 billion cigarettes last year. The German company of the third-largest international tobacco group has 1,800 employees. In view of this high productivity at speeds far above one’s own optical perception, nothing runs without the holding forces of the negative pressure.
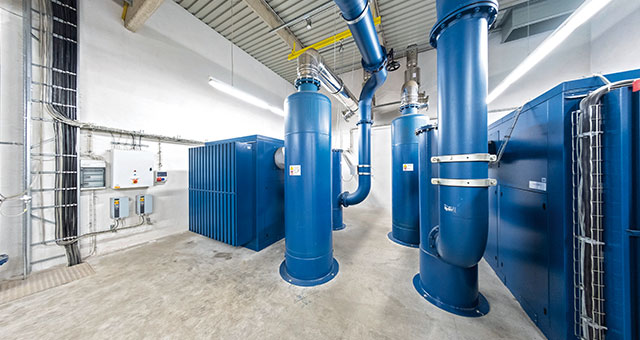
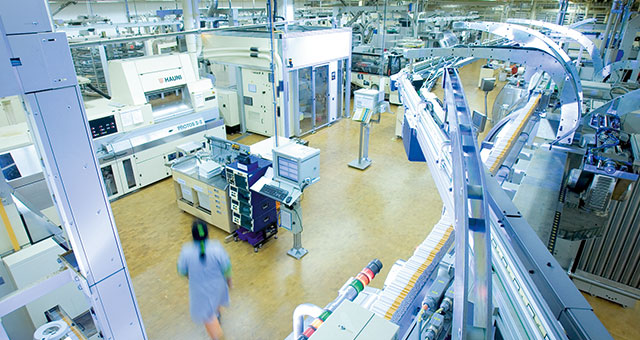
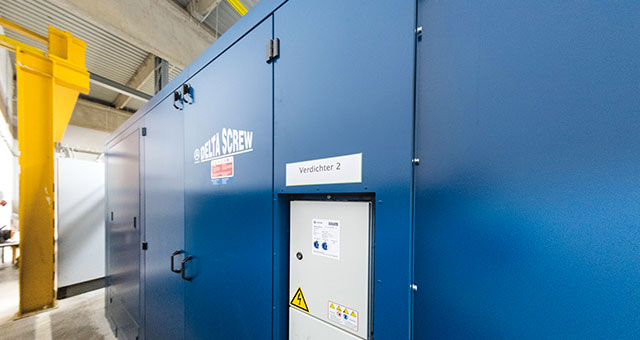
good that the same structure is also used in the JTI production plant on Tenerife.
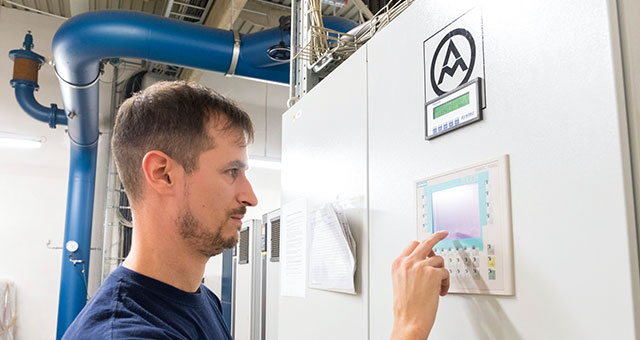
High speed with negative pressure
In order to appreciate the importance of the highly available and precisely set vacuum of around 340 millibars, it is worth taking a look at the processes of a cigarette machine. The high speed makes it impossible to implement hold and transfer functions. “At about 20,000 units per minute, centrifugal forces occur, which we have to counteract by holding them. Mechanical solutions would inevitably result in deformations, marks and damage to the sensitive cigarettes,” explains Arnhelm Köster. With a pressure corresponding to about one third of the atmospheric pressure usually prevailing, the cigarette paper is sucked from the roll outside to a contour so that it can lie around the round-shaped endless tobacco rolls. The paper is glued at the longitudinal seam and the finished cigarette rod is cut to length a little later. Vacuum is also necessary to connect the cigarette sections to their filters in a continuous process. These processes can be compared to a fast-rotating carousel system of cylindrical product carriers that synchronously transfer the cigarettes from one station to the next. The negative pressure acts through small holes in the bulges in which the cigarettes are located. In the interior of the cylinders are certain vacuum levels. They act as a seal between zones of different pressure.
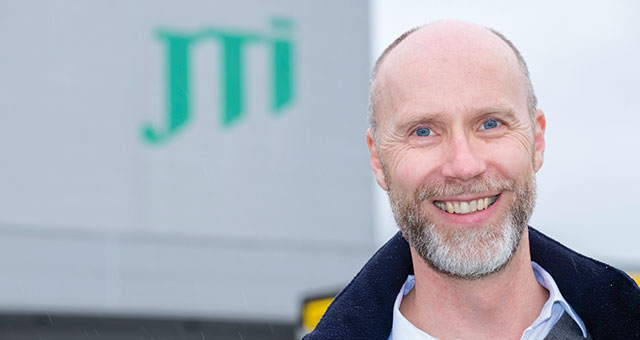
Arnhelm Köster, Head of Industrial Engineering at JTI in Trier:
"The assemblies should simply do their job over a long period of time."
AERZEN Delta Screws play a key role
The short insight into the principle of modern cigarette production makes the importance of vacuum generation clear. “And we need vacuum in large quantities,” emphasises Arnhelm Köster. JTI was looking for a new partner for this key function in the course of general modernisation and expansion of the plant, which is located in three central stations at the Trier plant. Today, two AERZEN Delta Screw screw compressors operate around the clock in station 3. It is the latest and also the one whose performance is used most. Two further stations with older devices are also connected to the vacuum network, but serve more redundancy in terms of operational safety. With this distribution of tasks, JTI ensures availability and maximum efficiency in three-shift operation. “Redundancy is just as important a topic in industrial engineering as energy efficiency.” The requirements profile for the compressors is derived directly from this for the head of industrial engineering: “I expect them to work efficiently, trouble-free and with low maintenance. The assemblies should simply do their job over a long period of time.”
Close project cooperation
The decision for AERZEN was the result of an extensive market analysis. In addition, there was a recommendation from colleagues at JTI Global Engineering. “We compare data such as energy consumption over the life cycle and look at reference projects.” In addition to energy efficiency, attributes such as high machine availability, numerous safety aspects and low maintenance requirements also count for the product portfolio of the machine manufacturer from Lower Saxony. The close cooperation with AERZEN Engineering did the rest to modernise and upgrade the vacuum supply quickly and smoothly. “There are companies that make good machines and there are companies that also make engineering around it - right up to the joint planning of projects. For example, when it comes to finding the best way to integrate the new technology into existing infrastructures,” the JTI Production Manager describes the positive cooperation. And communication is the first priority. “We talk the same language.” The success in Trier finally led to the fact that the same vacuum technology is now also in use in the JTI production plant on Tenerife.
The Delta Screws of type VML 95 are equipped on the Canary Islands as in Trier with a speed-controlled direct drive controlled by frequency inverter. With a drive power of 315 kW, each unit delivers a maximum volume flow of 5760 cubic metres with maximum energy efficiency. The necessary power requirement is directly coupled with pressure monitoring. The two VML 95 screw compressors are connected to a higher-level system by means of the AERtronic package control system. This gives JTI the possibility to operate the two machines optimally in combination. In addition, the way for machine monitoring is paved. “We want to know how our systems are doing and how well they are running,” says Ulrich Kirchen, energy system electronics engineer at JTI. The integration of the Deltra Screw VML95 in the control level clears the way for preventive maintenance and condition monitoring in real time. With the correct analysis of operating conditions and individual values, the operating technicians can make reliable statements as to when the filters connected between production and the screw compressor are so blocked that they have to be replaced. These steps are necessary to protect the Delta Screw screws from unavoidable dust or tobacco particles from production.
Result
A look at the industrial engineering at JTI shows how important complete systems, including close engineering cooperation, are in projects. Investment decisions are made less and less on the basis of individual machine prices, but on the basis of a detailed analysis of the total cost of ownership. Availability also plays a central role here, because production downtime in the event of a malfunction usually assumes a multiple value of what may initially have been saved when the machines were purchased.