Knauf
Pneumatic conveying: Knauf and Iss rely on screw compressors made by AERZEN
The energy revolution will make the gypsum industry increasingly dependent on natural stone deposits in the future. The entire industry is in a state of upheaval, because the FGD gypsum produced in the desulphurisation plants of lignite-fired power plants is a dying breed due to the shutdown of these power plants. On the other hand, the possible applications of gypsum are becoming more and more diversified for example: fire-retardant or water-repellent gypsum plasterboard, plaster, flowing screed and gypsum fibre board are just some of the applications in the construction industry. No industry can do without gypsum anymore. This makes it all the more important for leading manufacturers, such as Knauf, to use limited raw materials sparingly.
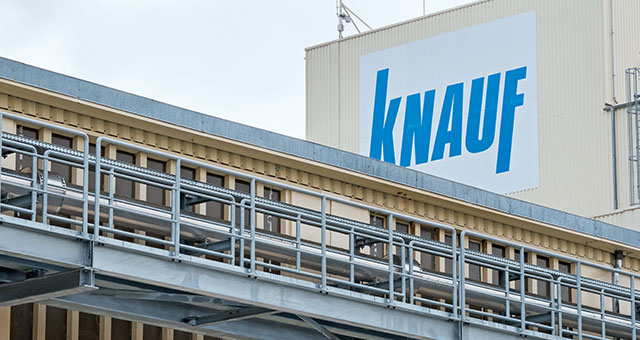
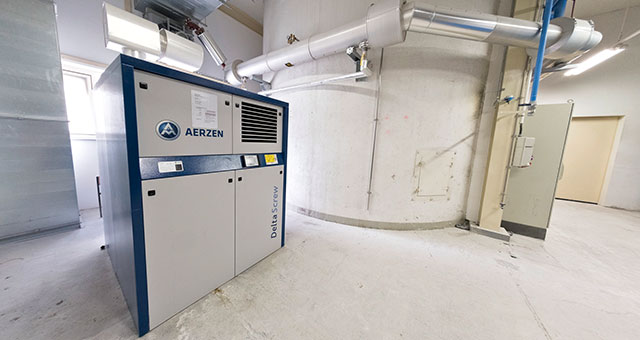
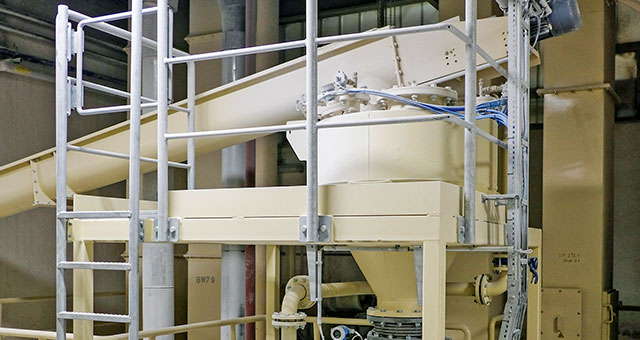
The hunger for gypsum
At the Rottleberode plant, for example, Knauf returns the edge breaks which occur during the production of gypsum fibreboard to the material flow in the same way as the dust during surface grinding. “Every crumb of gypsum is important for us. This is why raw materials should no longer be disposed of during production,” emphasises plant manager André Materlik. His company is the only one within the Knauf Group which exclusively processes natural gypsum from the quarries in the southern Harz region. In view of the move away from lignite mining, industry experts argue that only those companies which develop and secure mining areas in the long term will continue to exist – and demand for gypsum in Germany alone is already high at around ten million tonnes per year. According to Materlik, around 450,000 tons of finished product leaves the Rottleberode plant every year, with around 100 truckloads a day.
Stucco plaster, fine cellulose from waste paper and water: this is the mixture from which gypsum fibreboards are made. ISS Schüttguttechnik GmbH from Wilnsdorf in the Siegerland region plans and builds blow moulding machines to supply the mixers. ISS had already done a good job at Knauf before the new fibreboard plant was built, and had successfully got to grips with the problems involved in conveying and metering pulverised lignite. The fuel develops the necessary heat for calcining the rough stones. In the process, the natural gypsum loses a large part of its crystallised water content. “For uniform thermal processes, the constant transport of lignite without pressure or volume fluctuations is essential,” explains the plant manager. Any deviation from the ideal line is noticeable and can affect the product quality of the stucco, the deposits in the calcining mill, the CO values in the exhaust gas flow or the energy consumption of the screw compressors. “Uniform processes require less air,” says ISS Sales Managing Director Robert Partzsch, who speaks from experience.
Process-safe with high efficiency
For this reason, ISS has also put all of its know-how into the development of an overall solution for the conveying of stucco plaster, which was developed in Rottleberode together with the plant planners of Knauf Engineering GmbH. The company, under the Knauf umbrella, planned the entire new building at Iphofen and also ordered the conveyor technology. The main focus was on process safety, longevity and energy efficiency. „The high efficiency is due to the AERZEN screw compressors,“ says Partzsch. In addition, the Delta Screw series is recommended because of its pressure range, which is ideally suited for the transport of stucco.
It is important to know that according to the experience of the ISS Managing Director in the pneumatic conveying of bulk materials, compressed air with 5 to 6 bar is often first generated in order to feed an air vessel. This makes available an often significantly lower delivery pressure. “Intermediate buffering always results in energy losses,” emphasises Thomas Koch, head of technical mechanics at the Knauf plant in southern Harz. The Joule-Thomson effect is proof of this. Every 100 millibar increase in pressure causes a temperature rise in the compressed air of +10 degrees centigrade, due to the increased friction of the molecules. The effects of this physical connection can be limited if air vessels are dispensed with - as is the case at Knauf. However, since thermal energy cannot be completely prevented during pneumatic conveying, Knauf uses it in winter with recovery for heating purposes.
Never wasting any energy
In view of the fact that it is always better not to use electricity in the first place, rather than returning it later as heat, the goal must be to use compressors in energy-intensive compressed air that deliver the required volume flow with exactly the required pressure without intermediate storage. “AERZEN is simply the leader in the range from 2 to 3.5 bar,“ notes Partzsch and adds: „why should I generate 6 bars when I only need 3 bars?“
The Delta Screw units type VM21 with a motor rating of 90 kW supply a volume flow of 1,200 cubic metres per hour. The maximum pressure is 3.5 bar. The Generation 5 machines of the Delta Screw series installed at Knauf are designed by AERZEN as universal machines - with great attention to efficiency. Developed as a flexible modular system, the different compressor units can be suitably configured with motors of varying performance and an extensive range of accessories. Belt drive adjustment options, for example, provide the basis for accurately adjusting the volume flow even at fixed speeds - with the aim of preventing energy-intensive excess generation. This claim is backed up by the renunciation of redundancy at Knauf. Compressors and conveying systems work so reliably that separate „backup technology“ can be dispensed with. “The plant is designed for a capacity of twelve tons of gypsum per hour,” says Koch. If one assembly is taken off the grid, a temporarily switched bypass solution ensures reliability of supply. “However, our installation generally provides that one compressor always serves one system,” he adds.”
Result
In the course of building Knauf’s new fibreboard factory in the southern Harz, the newly installed blow moulding systems for pneumatic conveyance of stucco highlight some of the most important elements for minimising the consumption of costly energy - the focus was on increased efficiency and optimal design at the point of operation. Knauf has a clear system concept with the equipment at its works. “It is the combination of scientific and technical knowledge which makes up the solution of ISS. Here, everything is as it should be,” says plant manager Materlik.