Power consumption is reduced by 20 percent and, thus, a return on investment of just two to three years: the investment in new blower technology for the aeration is quickly paying off for the Erftverband. In 2019, the water and wastewater association started up a blower combination, consisting of two turbos and one rotary lobe compressor from AERZEN in the wastewater treatment plant Bergheim-Kenten, Germany. The constellation was the result of a comprehensive process air analysis as part of an AERaudit.
- Article One-fifth of energy saved in the aeration process
After modernisation, the Bergheim wastewater treatment plant pays €60,000 less electricity per year
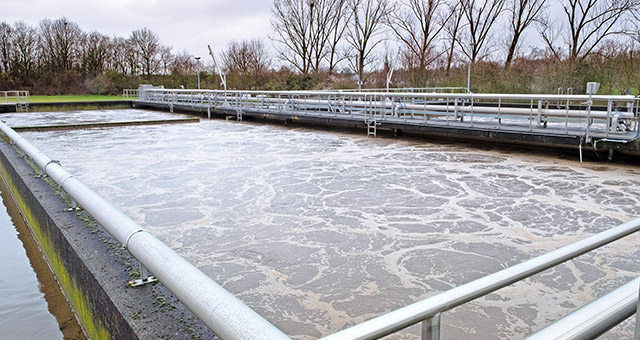
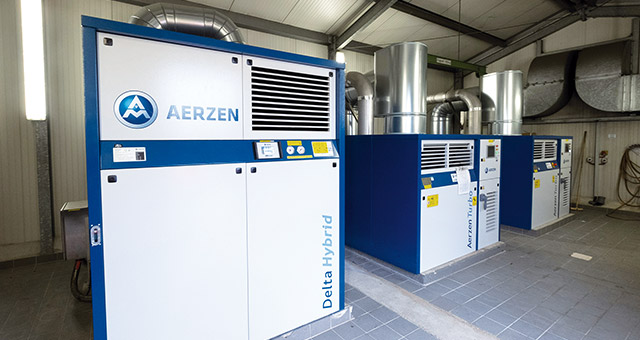
It was a suggestion for improvement made by the company’s own staff, which in future will ensure far-reaching energy savings at the Bergheim-Kenten wastewater treatment plant. When due to age the purchase of new blower technology was in the house, the team of wastewater master Ralf Herde and production engineer Günter Breuer used the opportunity to make an AERaudit together with AERZEN. The association, thus, abandoned its original plan to replace the old assemblies only with comparable, more recent technology. “We are tackling the heart of the wastewater treatment plant - the air supply for biology,” says Günter Breuer, explaining the value of the modernisation. In terms of equipment, this is now a combination of two turbo blowers of type AT 150-0.8S and one rotary lobe compressor of the type Delta Hybrid D62S.
This combination was the result of AERaudit, which in turn was based on a three-week measurement period. The parameters determined and put into context over time included mass flows, temperatures of media and the environment, differential pressures, power consumption and the associated voltages and currents. Here, AERZEN uses precise measuring transducers on all three phases with regard to the load capacity of the data, for example, upstream of the frequency inverter of the assemblies. A volume flow measurement was installed at the same time. The performance measurement revealed that with a new machine design, before modernisation, the average energy consumption of 3,590 kVh per day can be reduced to theoretically 2,232 kVh.
Incidentally, the forecast, which was then calculated by adding some correction aspects and 20 percent, proved to be reliable in the further course of the project. The actual figures are on the expected performance curve.
Especially with the base load on the ideal line
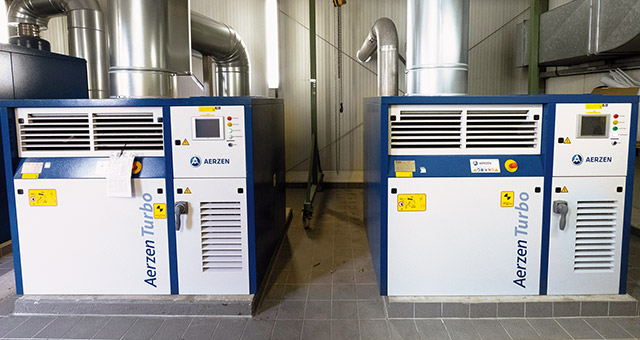
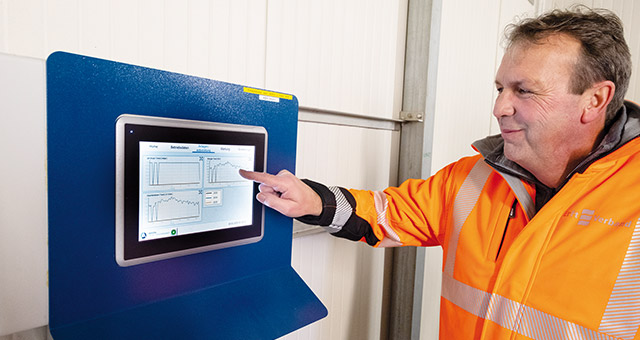
Turbo, turbo, Delta Hybrid rotary lobe compressor: the triad of AERZEN covers today in an ideal way the air demand of the Bergheim-Kenten wastewater treatment plant. In concrete terms, ideal means running the machines in such a way that they provide air in the aeration process at the optimum operating point - i.e. maximum efficiency. In the course of the AERaudit inventory, the required air volume was 4,200 standard cubic metres per tank and hour. The wastewater treatment plant has two aeration tanks. The turbos are designed for 5,000 standard cubic metres and can, therefore, ideally handle the normal load in terms of energy. If demand is far below this level, the Delta Hybrid takes over and the turbos are disconnected as base load units. If maximum performance is required due to high outside temperatures and COD load (Chemical Oxygen Demand), all three assemblies together reach 13,000 standard cubic meters. “Our experience shows that we need a maximum of 12,000 at the top. With this machine constellation we are, therefore, on the safe side,” says wastewater master Ralf Herde, reporting from experience.
Optimal energy supply to meet demand
Every load change in wastewater treatment results in a very different air requirement. In technical implementation, this statement led to the Performance³ strategy. The machine portfolio of the Lower Saxony company forms the basis for selecting the appropriate equipment combination of positive displacement blower, rotary lobe compressor and turbo on the basis of measured load curves and their proportion over an operating period.
The AERsmart control system regulates which assembly with which performance, together with whom or alone, provides sufficient air on the basis of the stored machine characteristics. In this way, AERZEN ensures that the air requirement of the aeration is always covered with the most energetically sensible technology - without losing sight of the wear and tear behaviour through constant switching on and off.
The efficient coordination of the combination is handled by AERsmart completely autonomously and independently of the process control level of the wastewater treatment plant. “We ourselves have nothing to do with the regulation,” says Ralf Herde happily. The wastewater master has been working on the 120,000 population equivalent plant for 20 years. This makes it the second largest of the Erftverband, which operates further 35 plants and employs 500 people on its 1,900 square kilometre area. In addition, there is an area of another 2,300 square kilometres where the Erftverband observes and researches the water management conditions in connection with opencast lignite mining. The area of responsibility, thus, extends from the Dutch border to the Rhine and from Neuss to Bad Münstereifel.
For Erftverband, the Performance³ approach and the analysis of operational data with AERaudit are trend-setting. Plant engineer Günter Breuer is convinced that the results of the model experiment have the potential to continue to be used beyond the company’s own supply area. “We are not a small company and maintain a close exchange of experience with neighbouring associations on a technical level.” Away from the technical possibilities of modern blower technology and the opportunities offered by integrated control system, Günter Breuer believes that the success of the modernisation is primarily due to the commitment of his team on site. “It’s worth looking closely to find the big screws worth turning.”