Generating process air is one of the most energy-intensive tasks in the field of industry. In view of climate change and the general striving for more sustainability, it is important to generate process air as efficiently as possible and, above all, to use it economically. The steady advance of digitalisation, with its new opportunities, offers excellent opportunities to make process air system more intelligent and their operation more transparent. To this end, AERZEN is bundling its know-how in a scalable Industrial Internet of Things (IIoT) platform called AERprogress.
- Article Digitised blower: Get more out of it, consume less
AERprogress: The new IIoT platform of AERZEN for greater availability and efficiency
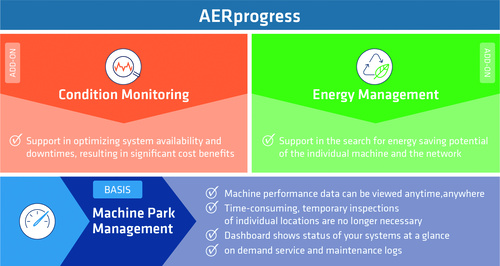
This is what it involves: using existing operating data, determining other key values with a targeted sensor technology and then condensing all of this into meaningful information. This creates the basis for optimised operation - including deducing measures that can achieve sustainability. This statement can be found in the current trend topics of blower technology: energy efficiency, monitoring and predictive maintenance. Instead of stuff-ing process air units with expensive sensor systems at this point, AERprogress primarily makes use of the signals and operational states already available via the control system. Supplemented by a few additional sensors, statements can be made on the probability of failures, operational states, trends and possible optimisations.
AERprogress stands for transparency
There is a lot involved in process air - both in terms of electrical energy as well as options for improving efficiency. One area of AERprogress is called “Machine Park Management” and forms the basic module. The primary aim is to achieve improvements across the board through intelligent net-working of all systems involved in process air. The rule here is that once you have found the ideal setting, you’ll want to keep it. For this purpose, the AERprogress basic module includes live monitoring for spatially independent online system management, among other things. Other functions are real-time reports at the push of a button and detailed maintenance and upkeep protocols. Overall, the basic package provides machine park management tools with which the availabilities and capacity utilisations of all connected machines can be analysed and modified - all of this on the premise of the greatest possible transparency.
Condition monitoring module
Based on the IoT solution “Machine Park Management”, AERZEN offers the service “Condition Monitoring” as an additional platform module. While the management functions primarily pursue the goal of optimising operations through a smart network, the core of condition monitoring is availability. The main concern here is ensuring operation through intelligent strategies for efficient maintenance and plannable maintenance.
The most economical way to maintain machines and systems is on a usage-ba-sis - taking into account, above all, the degree of wear and tear. Since wear and tear is directly dependent on how a system is operated, permanent recording and evaluation of the machine’s condition enables a statement to be made as to when it makes sense to initiate measures. The complex consideration of cause-and-effect relationships between the most diverse components within a process enables a complete status assessment of all technical systems. The service package is conceptually designed to avoid high prevention costs due to machine downtime, maintenance effort and redundancy.
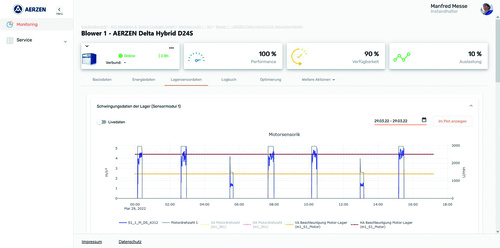
A classic example of the use of a CMS (Condition Monitoring System) is the monitoring of bearings with the help of temperature and vibration sensors. However, using the sensor data without reflection for an alarm system is insufficient. Rather, it must be possible to set limit values and map trends with a CMS. And if the literal red line is crossed, it does not necessarily have to indicate a failure. For example, the temperature of a bearing may be above its operating standard after maintenance work, since fresh oil was added. “The system sounds the alarm, but an expert still has to view the available data and know what they mean,” explains Jan Maksel, Product Manager of AERprogress. The same is true of vibration measurement. The available frequency curves can be used very effectively, for example, for status evaluation of ball or roller bearings.
The operator is provided with information on a secure data platform regarding when in all probability unplanned failure of a machine can be expected. Consequently, they are able to shut down its production in time, in order to avoid a total economic loss. This approach can also be used as an early warning system - ultimately also to gain time for ordering a service technician and the necessary spare parts. Jan Maksel: “Ultimately, the focus in CMS is on monitoring the data measured against a limit value - in order to then act in a time-saving and targeted manner.”
Optimisation: Where does the energy go?
Sustainability counts - especially when it comes to climate protection through a smaller CO² footprint. The energy management module is also designed for the long term. Energy savings can be achieved at the machine, system and network levels. The module covers the machine factors that influence consumption. Among other things, these include intake temperatures, differential and intake pressures and the condition of filter cartridges. The IoT platform validates excess consumption on the basis of the information collected, analyses load profiles, makes suggestions for energy efficiency and compares actual and target situations. Consequently, in this module the influences of load profiles, load distributions, standstill times and network efficiency rates on resource efficiency are applied. Avoiding waste, reducing life cycle costs and continuously monitoring a plant are three detailed aspects of optimisation.
Conclusion
AERZEN has bundled its know-how in blower technology with the new opportunities provided by digitalisation in AERprogress. The system’s openness also makes integration of the services in existing IT and cloud infrastructures possible.